CATL, a global leader in consumer lithium battery manufacturing, was faced with the challenge of processing large-scale industrial equipment data: its smart manufacturing workshops operate over 10,000 production devices and more than 1 million data collection points, generating over 10 million time-series data records every minute. The team conducted an in-depth evaluation of time-series databases InfluxDB and TDengine, ultimately choosing TDengine to build a next-generation data platform.
This solution not only tripled data write performance and reduced storage costs by 70%, but also significantly streamlined the cluster size from 50 servers in the original plan to just 10. It enables millisecond-level anomaly detection and equipment health analysis, providing a stable and efficient real-time data foundation for predictive maintenance. This article will provide a detailed analysis of the technical architecture, implementation path, and practical results in smart manufacturing.
Introduction
In building key applications such as prognostics and health management (PHM), product quality warnings, and controls for individual processes, a series of challenges have emerged for CATL: large-scale data collection, high requirements for configuration flexibility, and strong dependence on real-time computing capabilities. These challenges are mainly reflected in the following areas:
- Massive Data Storage and Processing Pressure: Thousands of devices on the production line generate tens of thousands of data records per second, pushing traditional relational databases to their limits with high write latency and rapidly escalating storage costs.
- Insufficient Real-Time Analysis Capabilities: Quality inspection and equipment health monitoring require response times in seconds, but the original system falls short in meeting these needs.
- Difficulty Integrating Multi-Source Heterogeneous Data: Production data, environmental data, and supply chain data are scattered across multiple systems, making unified analysis difficult to achieve.
Technology Selection and Comparison
To address the challenges encountered in actual operations, the Intelligent Controls team at CATL conducted an in-depth evaluation and comparison of several time-series databases. After considering multiple factors, including system stability, read/write performance, total cost of hardware and software, developer friendliness, and ease of maintenance, TDengine was ultimately selected as the platform solution.
TDengine demonstrated significant advantages in key areas such as data compression, ingestion speed, analytics efficiency, and distributed architecture. It not only outperformed other solutions across the board in the existing business scenario but also offers strong scalability to support future features and use cases.
CATL’s internal test results show that TDengine leads across all key metrics, with hardware costs at only 40% of those required by InfluxDB, as shown in the following table.
Metric | InfluxDB | TDengine |
---|---|---|
Ingestion speed | 280,000 points per second | 920,000 points per second |
Query latency (aggregating 100 million data points) | 1.2 seconds | 0.15 seconds |
Compression ratio | 55% | 17% |
CPU usage | 75% | 32% |
Implementation
CATL has extensively integrated advanced technologies such as Industrial Internet of Things (IIoT) devices, PLCs, sensors, machine vision, and AI into its smart manufacturing system to build a highly automated production process, enabling real-time monitoring and quality control throughout the manufacturing workflow.
PLC data generated by various types of equipment is collected through specific protocols depending on the equipment specifications. The IoT gateway then converts these different protocols and sends the data to the core IoT platform cluster via a broker. The platform cluster then writes the data into TDengine (time-series data), Oracle Database (relational data), and the alert system.
Thanks to TDengine’s powerful time-series data storage capabilities, all collected device data can be written to the database in real time, providing a stable and reliable data foundation for the MES system. Meanwhile, with the help of Grafana, this data can be intuitively visualized and analyzed, significantly improving the efficiency and intelligence of production operations and maintenance.
During data collection, the system supports dynamic configuration adjustments on demand, with management carried out at the PLC level. The data collection points within each PLC can be flexibly modified according to the actual needs of business departments. The overall system architecture is as follows:
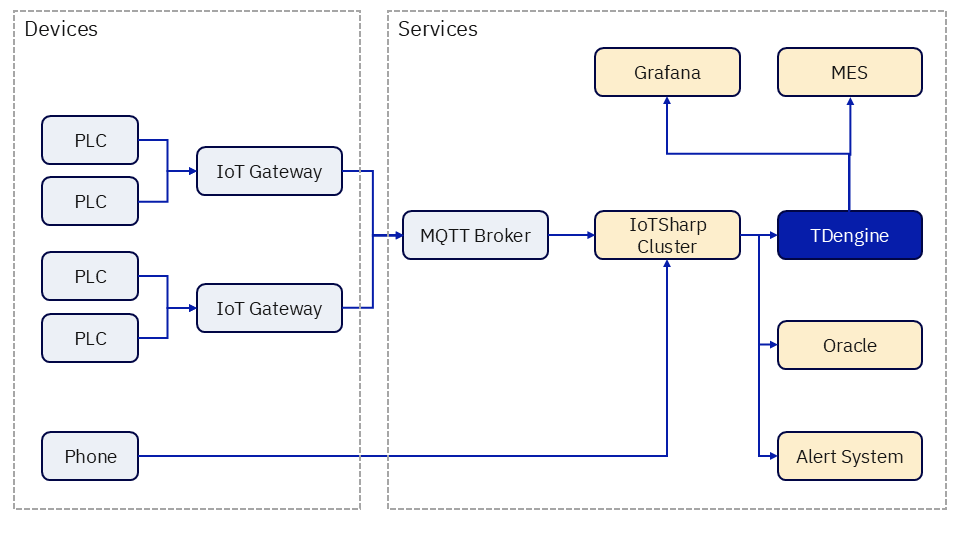
The current system uses a single supertable with the combination of “device name + parameter name” as the unique identifier for each subtable. In TDengine, data collection points can be added, modified, and deleted on demand, with the system automatically generating a dedicated subtable for each device during data ingestion. This enables “plug-and-play” data access, greatly enhancing deployment efficiency and flexibility.
Results
The production system supports data ingestion and storage for over 10,000 devices and more than 1 million data collection points in CATL’s smart manufacturing workshop, and their teams have developed programs in C# to write the data collected by the IoT platform into TDengine via SQL. The system writes over 8 million records per minute, with peak periods exceeding 10 million records per minute.
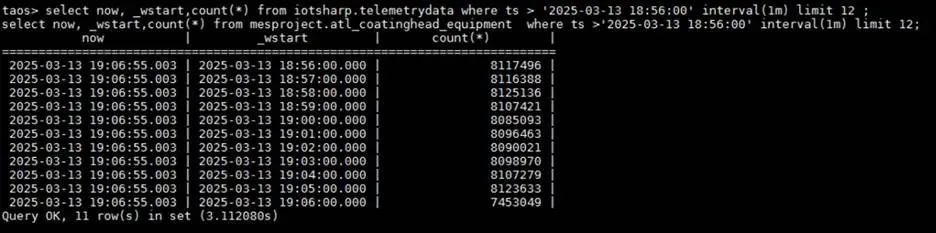
After being written into the production system, data is automatically synchronized to the UAT cluster. The production system retains data from the last 30 days to meet real-time and near-term query needs, while historical data older than 30 days is stored exclusively in the UAT system to support long-term analysis and historical queries. This strategy not only reduces storage costs but also significantly alleviates the query load on the production system.
Business Value
Deploying TDengine as its core time-series data platform helped CATL achieve comprehensive improvements in the following areas:
- Distributed Architecture Supporting High-Concurrency Ingestion: TDengine uses columnar storage and an innovative “one table per device” model, easily handling millions of data points per second. Its ingestion performance is nearly twice as fast as the original InfluxDB cluster.
- Efficient Compression Reducing Storage Costs: Powered by compression algorithms specifically designed for time-series data, TDengine reduces storage usage to one-third of that of InfluxDB, enabling long-term historical data retention and process traceability.
- Multi-Source Data Integration with Standard SQL Support: With TDengine’s schemaless ingestion capability, device logs and MES system data can be seamlessly integrated. Combined with standard SQL, this enables flexible cross-system analysis.
“TDengine helped us address the urgent challenge of processing massive volumes of time-series data. Its high performance and low resource consumption allowed us to ensure business continuity while advancing our data-driven smart manufacturing initiatives.”
— Technical Director, Smart Manufacturing Center, CATL
TDengine now monitors key metrics such as vibration and current for over 10,000 devices in real time, boosting predictive maintenance accuracy to 95% and providing a solid foundation for production stability and equipment health.
Future Plans
CATL is planning to expand the use of TDengine in key scenarios such as digital twins and AI-based quality inspection, aiming to build a comprehensive IIoT platform for the lithium battery industry and lead technological innovation in the renewables sector. Future plans include:
- Expanding TDengine deployment to five global production sites to establish a unified data platform architecture
- Integrating AI frameworks to enable millisecond-level process parameter optimization, driving intelligent upgrades in manufacturing
- Building a terabyte-scale time-series data sandbox for R&D teams to conduct modeling, validation, and algorithm training, unlocking the full potential of the data.